정밀 금속 부품은 다양한 정밀 가공 기술을 사용하여 제작되는 경우가 많으며, CNC 가공이 일반적인 방식입니다. 일반적으로 정밀 부품은 치수와 외관 모두에서 높은 기준을 요구합니다.
따라서 알루미늄이나 구리와 같은 금속을 CNC 가공할 때 완제품 표면에 공구 자국과 선이 발생하는 것이 문제가 됩니다. 본 글에서는 금속 제품 가공 시 공구 자국과 선이 발생하는 원인을 살펴보고, 이에 대한 잠재적 해결책을 제시합니다.
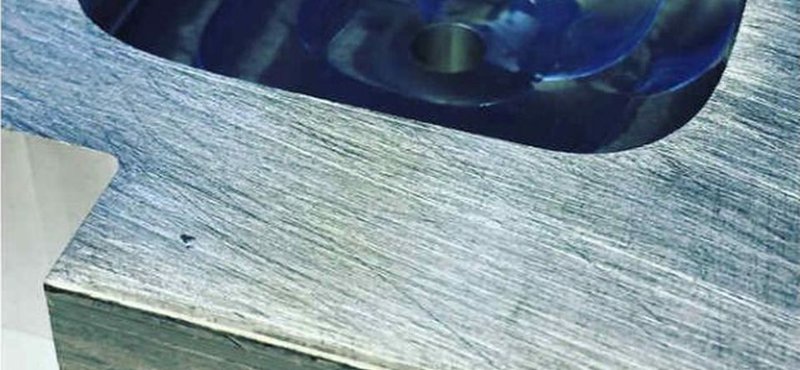
고정구의 클램핑력이 부족함
원인:일부 금속 캐비티 제품은 진공 고정 장치를 사용해야 하며, 표면 불규칙성으로 인해 충분한 흡입력을 생성하는 데 어려움을 겪을 수 있으며, 이로 인해 도구 자국이나 선이 생길 수 있습니다.
해결책:이를 완화하려면 단순 진공 흡입 방식에서 압력 또는 측면 지지를 결합한 진공 흡입 방식으로 전환하는 것을 고려하십시오. 또는 특정 부품 구조에 따라 대체 고정 옵션을 검토하여 특정 문제에 맞게 솔루션을 맞춤화할 수 있습니다.
프로세스 관련 요인
원인:특정 제품 제조 공정이 이 문제의 원인이 될 수 있습니다. 예를 들어, 태블릿 PC 후면 케이스와 같은 제품은 측면 구멍을 펀칭한 후 CNC 밀링으로 가장자리를 가공하는 일련의 가공 단계를 거칩니다. 이러한 공정으로 인해 밀링이 측면 구멍 위치에 도달할 때 눈에 띄는 공구 자국이 발생할 수 있습니다.
해결책:이 문제는 전자 제품 외피에 알루미늄 합금을 사용할 때 흔히 발생합니다. 이 문제를 해결하려면 측면 펀칭과 밀링을 CNC 밀링으로만 대체하여 공정을 수정할 수 있습니다. 동시에 공구의 일관된 맞물림을 보장하고 밀링 시 불균일한 절삭을 줄일 수 있습니다.
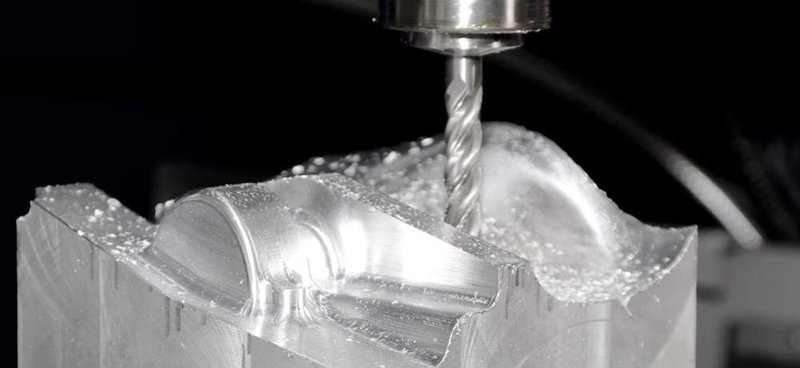
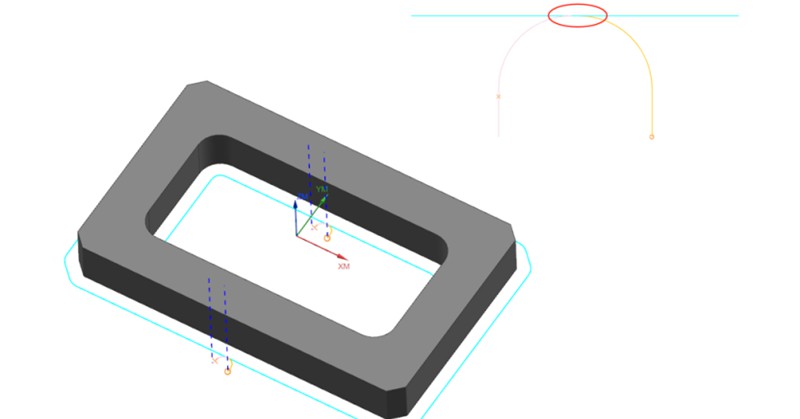
툴 경로 참여의 부적절한 프로그래밍
원인:이 문제는 제품 생산의 2D 윤곽 가공 단계에서 흔히 발생합니다. CNC 프로그램에서 공구 경로가 잘못 설계되어 공구의 진입점과 진출점에 흔적이 남습니다.
해결책:진입점과 출구점에서 공구 자국이 생기지 않도록 하는 과제를 해결하기 위해, 일반적인 접근법은 공구 결합 거리를 약간(약 0.2mm) 겹치게 하는 것입니다. 이 기법은 기계의 리드 스크류 정밀도에 발생할 수 있는 부정확성을 방지합니다.
이 전략은 공구 자국 형성을 효과적으로 방지하지만, 제품 소재가 연성 금속인 경우 반복적인 가공이 필요합니다. 결과적으로 이 부분은 다른 부위에 비해 질감과 색상이 다르게 나타날 수 있습니다.
평평한 가공 표면의 물고기 비늘 패턴
원인:제품의 평평한 표면에 물고기 비늘이나 원형 무늬가 나타나는 경우. 알루미늄/구리와 같은 연성 금속 가공에 사용되는 절삭 공구는 일반적으로 3~4개의 플루트를 가진 합금 소재 밀링 머신입니다. 경도는 HRC55~HRC65입니다. 이러한 밀링 절삭 공구는 공구의 바닥 가장자리를 사용하여 가공되며, 부품 표면에 독특한 물고기 비늘 무늬가 생겨 전체적인 외관에 영향을 줄 수 있습니다.
해결책:평탄도가 높은 제품이나 오목한 구조가 있는 평평한 표면에서 흔히 발생합니다. 해결책은 합성 다이아몬드 소재의 절삭 공구로 전환하는 것입니다. 이는 더 매끄러운 표면 마감을 얻는 데 도움이 됩니다.
장비 구성 요소의 노화 및 마모
원인:제품 표면의 공구 자국은 장비 스핀들, 베어링, 리드 스크류의 노화 및 마모로 인해 발생합니다. 또한, CNC 시스템의 백래시 매개변수가 부족하여 특히 둥근 모서리 가공 시 공구 자국이 심하게 발생합니다.
해결책:이러한 문제는 장비 관련 요소에서 비롯되며, 목표 지향적인 유지관리와 교체를 통해 해결할 수 있습니다.
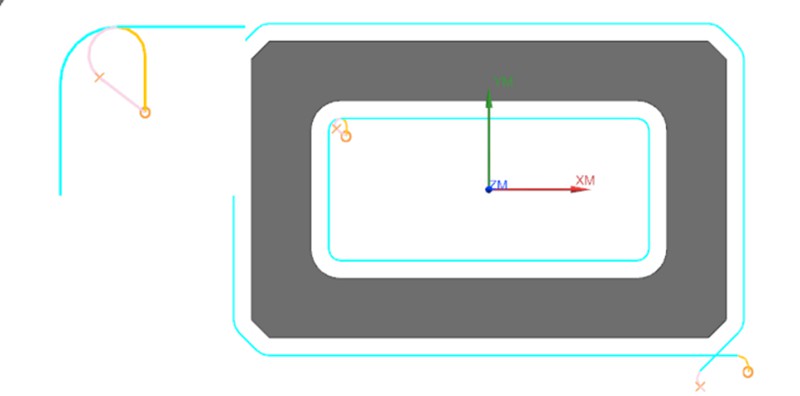
결론
CNC 금속 가공에서 이상적인 표면을 구현하려면 유용한 접근 방식이 필요합니다. 공구 자국과 선이 생기지 않도록 하는 다양한 방법이 있으며, 여기에는 장비 유지보수, 고정구 개선, 공정 조정, 그리고 프로그래밍 개선이 모두 포함됩니다. 제조업체는 이러한 요소들을 이해하고 수정함으로써 정밀 부품이 치수 기준을 충족할 뿐만 아니라 원하는 미적 품질까지 보장할 수 있습니다.